The recent COP28 deal on 13th December 2023 has committed over 200 countries to transition away from fossil fuels, signalling a clear call to action.
In the UK, decarbonising the UK housing stock plays a critical role in supporting this ambition to transition from fossil fuels. Heating systems are one of the UK's largest carbon emitters, responsible for nearly a third of the nation's annual carbon footprint1. The domestic heating sector alone contributes 17% of this total, a statistic that rivals the emissions generated by the entire fleet of the country's petrol and diesel vehicles2,3. When indirect emissions are factored in, this figure increases to 23%4.
However, the UK has one of western Europe’s oldest and leakiest housing stocks with around two thirds (19 million) of the total homes being rated EPC D and below, according to the Green Building Council. The UK government has outlined targets to achieve net zero by 2050, requiring a supply chain capacity to support over 2 million homes per-annum undergoing retrofitting by 2030. The next few years will be a short time horizon to prepare, invest and scale for mass market adoption and ‘whole-house’ decarbonisation.
In collaboration with TrustMark, Travis Perkins plc and WMG (Supply Chain Research Group) Warwick University, we have released a thought leadership report to explore the challenges and opportunities for the UK to meet the decarbonisation targets for the UK housing stock.
Our focus is on the supply chain and what is needed to address the needed scale-up is centred around three topics:
We have explored each element individually but also consider them as an integrated system that will need close alignment to achieve the UK’s decarbonisation targets.
1) Tackling the Green Skills Gap
The construction industry is grappling with a green skills-gap of approximately 270,000 tradespeople.
While there are various reasons for this, the primary contributor is the capability gap – not enough people have the basic green skills required to undertake retrofitting with proficiency. This is compounded by a volume gap – a growing demographic problem in which the existing workforce is retiring, and not enough people are entering the sector via the traditional apprenticeship route.
Within this topic we will look at:
- The role of regulation and policy in supporting upskilling for green homes and what is preventing the uptake in training
- What training and awareness is needed across the sector to address the capacity shortfalls
- The incentive case for trade-persons to move into green home retrofit from within the sector and bringing into the sector
- Regional differences and explore positive examples in action.
2) Quality standards and their importance for home decarbonisation
Standards and certifications give suppliers frameworks to abide by – in terms of their team’s capability, quality of work, customer service, and consumer protection. They also give assurance to customers and lenders that projects will be delivered to the right level of quality and sustainability.
However, to date, levels of understanding and take up of required certification ensuring quality standards in combination with skills and supply chain are not providing the assurance needed to support the necessary scale-up. A recent survey of small-medium enterprise trade businesses found that just 22% were aware of the PAS 2035 installer certification process required for scaling retrofit.
Within this topic we will look at:
- The evolution of government policy and the role TrustMark and others have had in developing quality standards to date
- The role of quality standards to foster consumer confidence and assurance to work being completed
- The barriers to adoption for quality standard certification and steps being taken to address this, including potential alternative points of entry for competent people
- Some key solutions to increase awareness and adoption.
3) Designing a sustainable materials supply chain for scale
The supply chain provides the technologies and materials required to make existing buildings more energy efficient and environmentally sustainable. The right skills and standards are required to design and deliver low carbon solutions, leveraging those technologies and materials. Scaling the supply chain for net zero brings complex issues surrounding sourcing, logistics, install coordination and sustainability.
In this final section, we look those challenges and how the industry, government, standards bodies, and other stakeholders can collaborate to overcome them.
Within this topic we will look at:
- The challenges on cost and early technology adoption creating barriers to scale
- The complexities in coordination of fragmented supply chains across a ‘whole-house’ retrofit and exploring solutions to address this
- The emergence of new business models and the need to ‘design’ the supply chains to deliver sustainable long-term material supply
- The role for UK manufacturing to support the scale-up.
To find out more, get in touch with David Mackenzie or Anjali Armstrong.
1 UK Parliament, Decarbonising heat in homes (February 2022).
2 Department for Energy Security and Net Zero, 2022 UK greenhouse gas emissions, provisional figures (March 2023).
3 Department for Business, Energy, and Industrial Strategy, Heat and buildings strategy (October 2021).
4 Climate Change Committee, The sixth carbon budget.
Related Insights
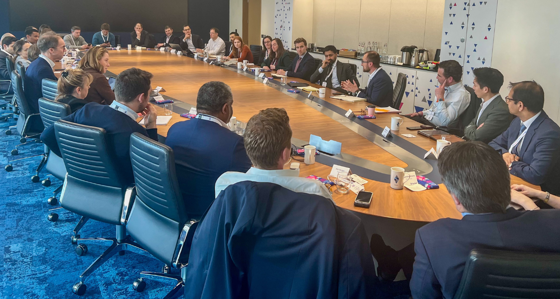
The hydrogen investment challenge
Incorporating learnings from early projects and overcoming barriers to financial close
Read more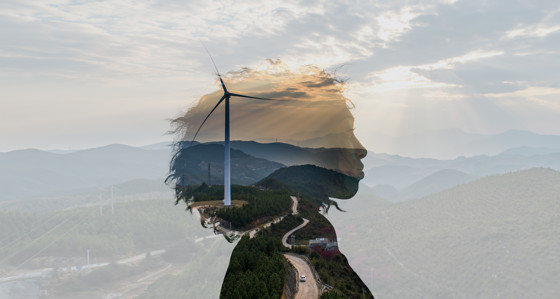
European power market outlook 2024
While the European power market has been significantly impacted by the Russian invasion of Ukraine, policy responses and higher-than-expected volumes of liquefied natural gas (LNG)—replacing Russian pipeline gas volumes—have reduced some of the expected impact. Read our latest power market outlook to understand the opportunities
Read more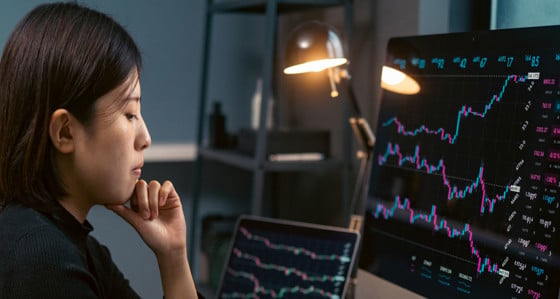
Commodities and energy trading video series
Join us as we delve into key areas that are shaping the trading industry
Read more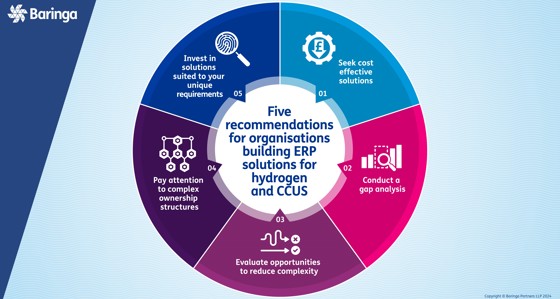
Powering the energy industry’s green future: Five recommendations for building ERP solutions for hydrogen and CCUS
Hydrogen and CCUS companies are ideally positioned to shape energy’s new digital future. But there are key areas of uncertainty that are preventing companies from taking final investment decisions.
Read moreRelated Case Studies
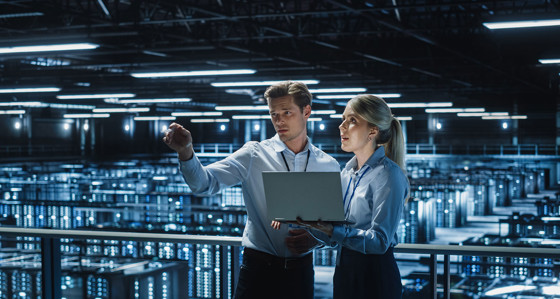
Shaping a self-generation strategy for a major data centre
How do you develop an energy generation plan that balances sustainability with commercial due diligence?
Read more
Evaluating the case for the world’s biggest offshore wind project
We helped our client reach financial close for all three phases of the project, securing 15-year CfDs with delivery between 2023-2025.
Read more
Green Hydrogen value-chains unpacked
Mapping and analysis of the potential of Green Hydrogen across multiple European markets helped our client’s strategic focus and investment decision-making.
Read more
Working with Netbeheer Nederland, we helped the Netherlands’ grid get to grips with solar
New solar panels are installed across the Netherlands daily. Each one is a step towards a greener energy system but only if that system is set up to use them.
Read more